All published articles of this journal are available on ScienceDirect.
Investigating the Dynamic Creep and the Tensile Performance of Zeolitic Tuff-modified Warm Asphalt Mixtures
Abstract
Aims
This research investigates the effect of adding natural Jordanian Zeolitic tuffs to the SUPERPAVE asphalt mixture at the dynamic creep and the indirect tensile performance.
Background
Rutting and fatigue are considered the most common types of distress that affect pavements all over the world. Many factors can affect these properties, such as different aggregate properties, asphalt grades, and properties, as well as the type and amount of the mineral filler. Mineral fillers play an important role in enhancing the asphalt mixtures' performance by filling the voids in the mixture besides improving the cohesion of the binder as it has a small weight in addition to a very large surface area. Generally, the powder of limestone is the most used type of filler. However, studies showed that many materials could also be used as mineral fillers successfully. The focus of this study is using natural Jordanian Zeolitic tuff as a mineral filler. Jordanian zeolitic tuff mainly consists of Phillipsite, chabazite, and faujasite, which are considered the most abundant Zeolitic tuff minerals. The pyroclastic material is widely distributed in the Badia region of northeast Jordan. Zeolitic tuffs are located in Jabal Aritayn (30km northeast of Azraq), Tlul AlShahba (20 km east of Al Safawi), Tal Al-Rimah (35 km northeast of Al Mafraq), and other small deposits in central and south Jordan.
Objectives
The aim of this research was to study the impact of Zeolitic tuffs on overall Superpave asphalt mixture performance.
Methods
The specimens were prepared using the optimum asphalt content obtained by the SUPERPAVE method. Dynamic Testing System DTS-16 was used to apply both dynamic creep and indirect tensile tests that give a good idea about the rutting and fatigue behavior of asphalt mixtures. Both tests were conducted at 25 °C.
Results
The Zeolitic tuffs modified asphalt mixtures have lower accumulated strains and higher creep stiffness compared to the control mixture. Subsequently, the indirect tensile test results showed that the modified asphalt mixtures have a higher resilient modulus than the control asphalt mix. Generally, using Zeolitic tuffs as a modifier of asphalt mixtures enhanced the rutting and fatigue resistance. The results showed that asphalt mixtures fortified with 25% Zeolitic tuffs emerged as the best contenders for rutting resistance. Also, mixtures enriched with 50% Zeolitic tuffs stood out in fatigue resistance performance.
Conclusion
The best dynamic creep performance was by adding 25% Zeolitic tuffs by the mineral filler mass, while the best resilient modulus was by adding 50% Zeolitic tuffs by the mineral filler mass.
Other
The overarching goals encompass understanding the dynamic creep behavior of Zeolitic tuff-infused asphalt blends, deciphering its indirect tensile performance, pinpointing the ideal replacement ratio for mineral fillers, and drawing a performance comparison between WMA and conventional Hot Mix Asphalt (HMA) compositions.
1. INTRODUCTION
As urban landscapes expand and transportation networks grow, pavements worldwide increasingly confront distresses such as rutting and fatigue. These challenges are compounded when factoring in the looming specter of climate change, which has introduced an array of strain-inducing variables, such as thermal cracking resulting from shifting climatic patterns. Such global challenges arise from diverse determinants that span variations in aggregate properties, the intricacies of asphalt grade and properties, and the strategic choice of mineral filler type and proportions. Recent studies, such as that by Liu et al. [1] have delved deep into the correlations between climate change and pavement issues, pointing to the alarming rise of thermal cracks, altered fatigue life, and rutting. Their research accentuates the urgency of preemptive adaptation measures, ranging from revising structural thickness modulating dynamic modulus to tweaking creep stiffness, especially in contexts like China.
At the heart of these global challenges and pivotal to facilitating the performance of asphalt mixtures stands the often-underestimated role of mineral fillers. These fillers, with their unique high surface-area-to-weight ratio, serve a dual purpose: filling the inherent voids in mixtures and bolstering the cohesion of binders. While limestone powder has historically been the go-to choice, the ever-evolving research landscape hints at a wider gamut of materials that could serve as effective mineral fillers.
In the context of Jordan, an innovative and locally sourced alternative emerges in the form of Zeolitic tuff. Jordan's rich geological tapestry, especially in regions like the Badia, offers an abundance of this mineral. Given its distinct properties and abundance, Jordanian Zeolitic tuff presents a regional solution and potentially a global alternative in the ever-pressing quest for sustainable and resilient pavement solutions. This research aspires to contribute to this discourse, grounding its findings in Jordan's unique geology and the universal challenges climate change poses to pavement infrastructures.
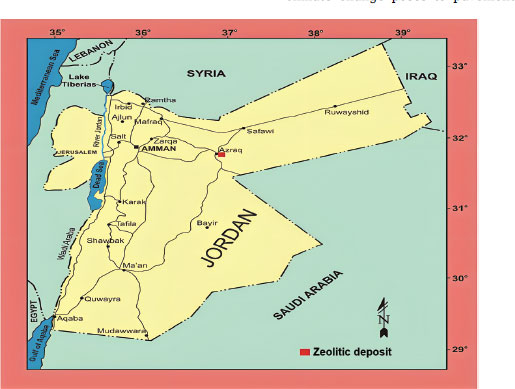
This investigation is squarely focused on the viability of Jordanian Zeolitic tuff as an innovative mineral filler in pavement engineering. Indigenous to Jordan and abundant in its natural reserves, Zeolitic tuff is predominantly characterized by Phillipsite, Chabazite, and Faujasite minerals. The Badia region, situated in northeast Jordan, emerges as a veritable epicenter for this volcaniclastic sediment, boasting significant deposits in locales such as Jabal Aritayn, Tlul AlShahba, and Tal Al-Rimah, extending even to areas in central and southern Jordan. The geographical distribution of these Zeolitic tuff reservoirs is meticulously illustrated in Fig. (1).
The trajectory of mineral filler evolution can be traced back to the duality between natural and manufactured sources. The former encompasses crushed stones, while the latter focuses on lime, cement, and slag. Since fillers constitute one of the most significant expenses in asphalt mix formulations, it is paramount to uncover alternatives that judiciously combine economic feasibility with enhanced performance [2].
A deep dive into previous research reveals an invigorated interest in these alternative fillers, both from an environmental conservation angle and an economic prudence perspective. Moreover, the ultimate aim is invariably to achieve superior mechanical characteristics in asphalt blends. The research conducted by Asi and Assa’ad [3] exemplifies this, showcasing the eco-beneficial aspects of integrating fly ash, often deemed an environmental nuisance, into Jordan's asphalt compositions. In a parallel vein, researchers such as Tapkin [4, 5] and Bani Baker et al. [6] have accentuated the potential of materials like fly ash and natural bentonite clay in amplifying asphalt performance metrics.
Navigating further, the fine-tuned equilibrium between the mineral filler's nature and its proportion has been aptly emphasized by Diab and Enieb [7]. Their insights crystallize the pivotal role fillers play in dictating the mechanical properties and the subsequent deformation behavior of the asphalt mixes. Pioneering works by Oreskovic et al. [8] and Woszuk et al. [9] have further broadened the horizon, unearthing the unique characteristics of Zeolitic tuffs and their promising utility in asphalt formulations.
Zeroing on Jordan's natural reserves reveals Zeolitic tuff, a noteworthy mineral. It primarily consists of Phillipsite, Chabazite, and Faujasite, making it a distinctive geological feature in regions such as the Badia in northeast Jordan. Notably, Zeolitic tuffs grace regions like Jabal Aritayn, Tlul AlShahba, and Tal Al-Rimah, with smaller deposits even found in central and southern parts of the country. These deposits, as shown in Fig. (1), hint at a promising avenue for sustainable pavement solutions, especially in light of the increasing global challenges faced by pavements.
This academic endeavor seeks to harness the potential of Zeolitic tuff in asphalt mixtures, aiming for Warm Mix Asphalt (WMA) modifications. The overarching goals encompass understanding the dynamic creep behavior of Zeolitic tuff-infused asphalt blends, deciphering its indirect tensile performance, pinpointing the ideal replacement ratio for mineral fillers, and drawing a performance comparison between WMA and conventional Hot Mix Asphalt (HMA) compositions.
1.1. Study Objectives
Jordanian Zeolitic Tuff in the Limelight
This study aims to:
1. Harness natural Jordanian Zeolitic tuff in modifying asphalt mixtures to produce Warm Mix Asphalt (WMA).
2. Examine the dynamic creep performance of such modified mixtures.
3. Investigate the indirect tensile performance of Zeolitic tuff-enhanced mixtures.
4. Determine the optimal percentage for replacing traditional mineral filler with Zeolitic tuffs.
5. Contrast the efficacy of WMA against standard Hot Mix Asphalt (HMA) mixtures.
We aspire to contribute significantly to the ongoing discourse on sustainable and efficient pavement solutions by anchoring our research to these objectives. Also, this research illuminates the myriad benefits of Zeolitic tuffs in warm asphalt mixtures and underscores the imperative of continued exploration in this domain.
1.2. Legal Framework in the Jordanian Construction Industry
Jordan's construction sector is a complex tapestry woven with challenges and prospects. Factors ranging from unplanned deviations, unforeseen changes in deliverables, and volatile material costs to management and communication breakdowns can significantly impact the trajectory of a project. Amidst this complexity, there is a recognized imperative for robust cost management, combined with the application of innovative techniques and technology for efficiency [10].
Jordan's dedication to environmental conservation sets it apart. In 1991, Jordan positioned itself as the pioneering Middle Eastern country to establish a national environmental agenda. This blueprint sought to marry the nation's growth aspirations with the critical preservation of its environmental resources. Key legislation like the Temporary Environmental Protection Law No. (1) Of (2003) and the Environmental Protection Law No. (6) of 2017 underpin this commitment. However, there are still concerns about certain legislative gaps, particularly around defined civil liabilities and the clarity of legal jurisdictions for environmental infractions [11].
The realm of construction in Jordan is multifaceted, marrying environmental considerations with stringent stipulations on safety, quality, and materials. The foundational Jordanian Construction Law demarcates the protocols for construction endeavors, highlighting the need for seasoned professionals and unwavering adherence to benchmarks. Integral to this framework are building permits, which undergo a thorough review by local bodies to verify their alignment with prevailing environmental and safety norms.
The centrality of safety is underscored in contracts, putting the responsibility squarely on general contractors to meet all stipulated safety protocols. This commitment cascades to subcontracts, necessitating alignment with the safety benchmarks the lead contractor sets, ensuring a unified commitment to safety at every project tier [12]. However, a discrepancy exists. While Jordan boasts a myriad of sustainability-focused construction regulations, like the National Environmental Strategy and Energy Efficient Building Codes, their adoption is often discretionary and needs more rigorous oversight [13].
The rising prominence of knowledge management in the Jordanian construction landscape underscores the value of collaborative knowledge dissemination and transparent communication [14]. In tandem, the emphasis on sustainable procurement, encompassing a broad spectrum of strategies, policies, and rules, aims to elevate project delivery standards [15]. This all-encompassing procurement approach guarantees alignment with pertinent legal frameworks, cultivating a more robust and green construction domain [13].
2. METHODOLOGY
All details on cite location, data collection, and analysis are presented in this section. Fig. (2) provides a streamlined illustration of the study's methodical experimental progression:
2.1. Stage 1
This foundational phase was dedicated to the diligent collection and intricate physical assessment of the materials. Every material was thoroughly characterized, not just by its inherent properties but also by its potential influence and relevance to the overarching objectives of the study.
2.2. Stage 2
Asphalt mixtures took shape through the precision-driven SUPERPAVE gyratory compactor (SGC). The focal point of this stage was the accurate determination of the Optimum Asphalt Content (OAC). Adopting the SUPERPAVE technique was not arbitrary; its recognized rigor and pinpoint accuracy guarantee optimal compaction, establishing a dependable foundation for the subsequent stages of the study.
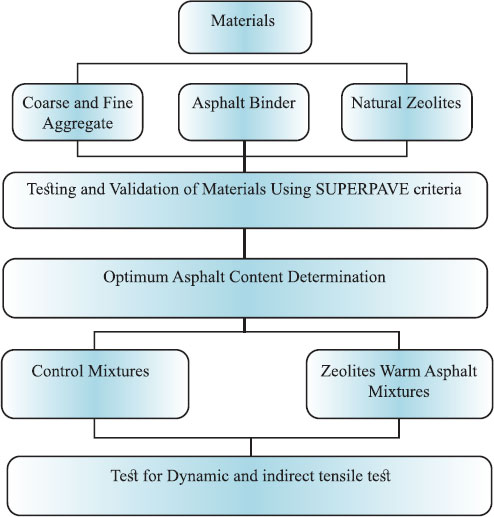
2.3. Stage 3
This culminating phase delved deep into the performance metrics of the SUPERPAVE asphalt concoctions. Emphasis was placed on two pivotal tests: the dynamic creep, which serves as a barometer for rutting, and the Indirect Tensile test, the litmus test for fatigue endurance.
2.4. Materials Used
In this study, three materials are used as follows:
2.4.1. Asphalt Binder
Specially chosen for its widespread adoption in Jordan's flexible pavement construction, this research harnessed the qualities of an Asphalt binder with an AC 60-70 penetration grade. This high-grade binder was procured from the renowned Jordan Petroleum Refinery Company (JPRC) in Zarqa, Jordan.
2.4.2. Aggregate
The study maintained quality when it came to limestone aggregates. They were subjected to meticulous testing through time-tested traditional methodologies and the more contemporary SUPERPAVE approaches. While the traditional tests, including specific gravity and LA abrasion assessments, illuminated the inherent properties of the aggregate, the SUPERPAVE tests, encompassing evaluations like F&E particles and Sand Equivalent, shed light on the broader consensus properties. All these findings have been systematically cataloged in Table 1, serving as a quick reference for the aggregate's characteristics.
2.4.3. Zeolitic Tuffs
More than just a mineral composite, Zeolitic tuffs are a symphony of aluminum silicate, sodium, calcium minerals, and water. Whether found in nature's embrace or sculpted in industrial settings, their importance cannot be overstated. The Jordanian strain, celebrated for its unmatched purity and bountiful reserves, stands out with its distinctive atomic framework that translates to tangible environmental benefits. One of the most significant advantages is the potential to slash the production temperatures of asphalt mixtures, curtailing emissions. Tables 2 and 3 offer a deep dive into the physical and chemical nuances of the Zeolitic tuff used in this research. Meanwhile, Figs. (3 and 4) visually decode the intricacies of the Zeolitic tuff, amplifying its significance and connection to the study.
Test | Coarse Aggregate | Fine Aggregate | Criteria |
---|---|---|---|
Gsb | 2.644 | 2.562 | NA |
Gsd | 2.703 | 2.616 | NA |
Gsa | 2.808 | 2.708 | NA |
Absorption (%) | 2.2% | 2.1% | NA |
LA (%) | 26% | NA | Less than or equal to 35% |
CAA (%) | 98/96% | NA | 95/90% |
FAA (%) | NA | 51% | More than or equal to 45% |
Flat and Elongated (%) | 3% | NA | Less than or equal to 10% |
SE (%) | NA | 66.7% | More than or equal to 45% |
Parameters | Range |
---|---|
PH | 7-8 |
Water absorption (%) | 9.7 |
unit weight (kg/m3) | 990 |
Voids ratio (%) | 25 |
Porosity (%) | 25 |
Soundness (%) | 8.5 |
thermal stability (Cº) | 300-600 |
Parameter | Percentage | Parameter | Percentage |
---|---|---|---|
SiO2 | 41.3 | P2O5 | 0.9 |
Al2O3 | 12.1 | MnO | 0.2 |
Fe2O3 | 13.6 | SO3 | 0.2 |
CaO | 9.8 | LOI | 8.5 |
MgO | 7.1 | Mo ppm | 2.4 |
K2O | 1.7 | Cu ppm | 36.3 |
Na2O | 2 | Zn ppm | 149.4 |
Tio2 | 2.8 | Total | 100% |
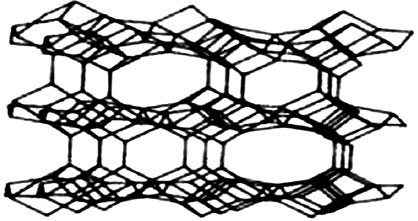
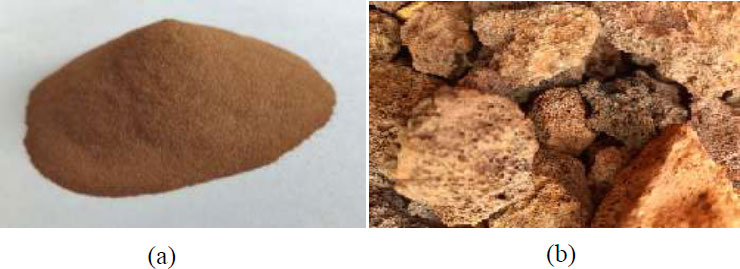
2.5. Performance Tests
The Asphalt Institute's pioneering efforts in performance tests began in 1993, emphasizing the evolution and critical analysis of SUPERPAVE mix designs. Originally, the central objective of these tests was to forecast the susceptibility of pavements to distress over varying durations and traffic intensities. However, with recent studies revealing certain prediction discrepancies, there has been a renewed emphasis on understanding the intrinsic mechanical properties that gauge the durability and resilience of asphalt mixtures, especially concerning rutting [17].
2.5.1. Dynamic Creep Test
A cornerstone in assessing rutting resistance, this test meticulously measures deformation under designated stress parameters. The findings delineate into three pivotal zones of deformation behavior. Fig. (5) offers a comprehensive visual representation of these zones, shedding light on the rutting tendencies of the tested mixtures [18].
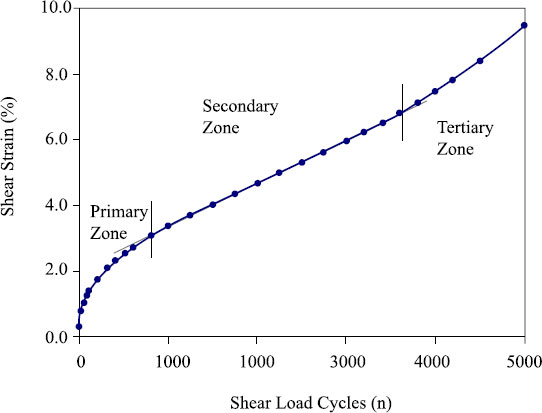
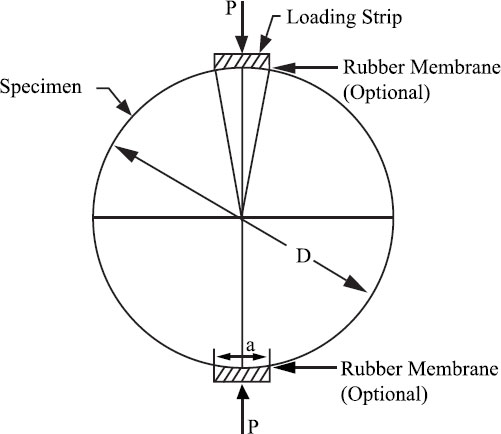
2.5.2. Indirect Tensile Test
The test was designed to evaluate the anti-cracking efficacy across a spectrum of temperatures, and this test applies compressive forces to cylindrical samples. A groundbreaking approach by Brown et al. [18] highlighted a diagonal load application's effectiveness, ushering in a swifter and more precise testing phase. Fig. (6) vividly depicts the testing configuration. A notable advantage of this methodology is its potential to mitigate binder aging, subsequently amplifying the fatigue resistance of WMA mixtures.
3. RESULTS AND DISCUSSION
The impact of incorporating Zeolitic tuffs into asphalt mixtures was meticulously assessed. This section offers an in-depth comparison between the properties of the standard control mixture and those modified with different percentages of Zeolitic tuffs.
3.1. Dynamic Creep Results
In an intricate and carefully orchestrated experiment, a total of ten specimens underwent rigorous testing under the dynamic creep apparatus, specifically the DTS-16. These tests were consistently conducted at an unwavering temperature of 25 Cº. Our attention was primarily riveted on two significant metrics: the accumulated micro-strain and the creep stiffness. These parameters are quintessential, shedding light on a mixture's potential susceptibility to rutting, common, and concerning pavement distress.
3.2. The Accumulated Micro-strain
The metric of accumulated strains serves as a beacon, illuminating the resilience of an asphalt mixture against rutting. It intricately maps the damage trajectory as it unfolds across various load cycles. A paramount observation is that reduced accumulated strain often signals enhanced resistance against rutting. Fig. (7) masterfully depicts the accumulated micro-strain trajectory upon completing 20,000 load cycles to offer a tangible perspective. This portrayal encompasses both the benchmark control and the mixtures enriched with Zeolitic tuffs, tested at a temperature of 25 Cº under a frequency of 8 Hz. For those craving a more holistic view, Fig. (8) methodically presents the accumulated micro-strain values for every specimen tested.
Delving deep into Figs. (7 and 8) unveils a prevailing narrative: asphalt mixtures augmented with Zeolitic tuffs mostly register diminished accumulated strains in juxtaposition with the benchmark control mixture. However, an outlier emerges the specimen boasts a composition laden with 100% Zeolitic tuffs. When juxtaposed, the accumulated strain for our foundational control mixture was discerned to be 300 µɛ. Intriguingly, with the infusion of 75%, 50%, and 25% Zeolitic tuffs, this value plummeted by 20%, 33%, and 43%, respectively. In stark contrast, a specimen with a composition dominated by 100% Zeolitic tuffs saw a surge in strain by 34%. The unique cementitious prowess of the Zeolitic tuff plays a pivotal role in bolstering the creep resistance of the asphalt concrete amalgamations. However, a pertinent observation is that the specimen infused with 100% Zeolitic tuffs lacked the uniform compaction evident in its peers. This variance in compaction undeniably influenced its strain accumulation and, by extension, its propensity for rutting. It is noteworthy that the mixture imbued with 25% Zeolitic tuffs emerged as the frontrunner in terms of rutting resistance at 25 Cº, resonating harmoniously with previous scholarly explorations on Warm Mix Asphalt (WMA) enriched with Zeolitic tuffs [19-21].
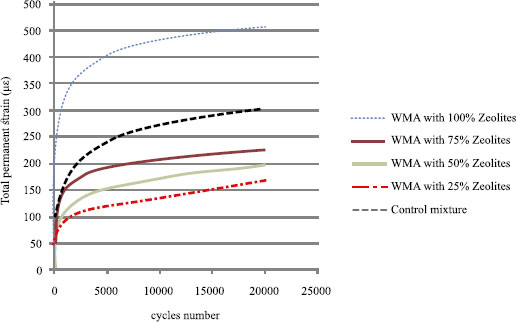
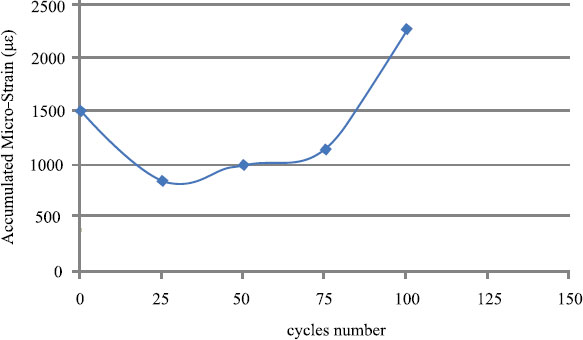
3.3. Creep Stiffness Modulus
The creep stiffness modulus, an indispensable metric in material science, elegantly captures the intrinsic nature of a material's resilience against deformation. It is eloquently articulated as the proportionality between the exerted stress and the consequent accumulated strain. To paint a vivid picture, Fig. (9) meticulously delineates the variance in the creep stiffness modulus as a function of diverse Zeolitic tuffs concentrations, all measured at a constant 25 Cº. For a more granular understanding, Fig. (10) unfurls the Creep Stiffness Modulus magnitudes for each specimen upon the culmination of the testing phase.
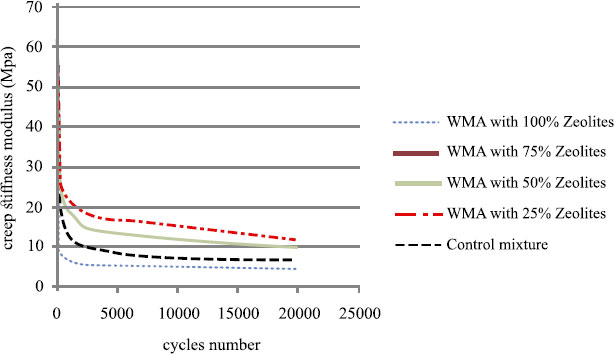
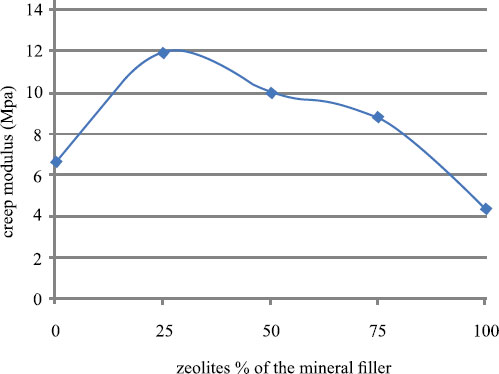
A deep dive into Fig. (9) reveals a telling narrative: the foundational control mixture's modulus hovers around the benchmark of 7. However, this narrative turns riveting when examining the Zeolitic tuffs-enriched mixtures. Mixtures infused with a concentration gradient of 25-75% Zeolitic tuffs audaciously transcend this benchmark. On the other end of the spectrum, a concoction dominated by 100% Zeolitic tuffs sees this modulus gracefully descend to a value of 4.5%. This observed trajectory is a testament to the transformative potential of Zeolitic tuffs. When integrated into mixtures, they usher in heightened resistance against rutting, a narrative that harmoniously resonates with insights from prior academic explorations [19-21].
3.4. The Synthesis of Zeolitic Tuffs within Asphalt Frameworks
Incorporating Zeolitic tuffs into asphalt mixtures is not just an arbitrary amalgamation but a well-thought-out endeavor. Including heralds marked enhancements in the resistance to rutting, a persisting challenge in pavement design. The blend with 25% Zeolitic tuffs is particularly remarkable, which emerges as a gold standard in rutting resilience. However, the tale is not one-dimensional. While the results are a testament to Zeolitic tuffs' transformative capabilities, they also underscore the essence of meticulous specimen preparation. Anomalies like the specimen with 100% Zeolitic tuffs deviate from the trend and sound an alert on the importance of uniform compaction.
Furthermore, to ensure a nuanced understanding, one must juxtapose these observations with the backdrop of existing literature. While this study echoes sentiments from previous research endeavors – lauding the merits of Zeolitic tuffs in enhancing rutting resistance – it's essential to discern those studies' methodological nuances and contextual specifics. This would offer a 360-degree view, ensuring that the inferences drawn are robust and relevant in the broader canvas of asphalt research.
CONCLUSION
This research undertook an exhaustive laboratory analysis, focusing on the efficacy of warm asphalt mixtures, specifically assessing the influence of varying percentages of Zeolitic tuffs. This analysis was juxtaposed against control HMA mixtures, which lacked the inclusion of Zeolitic tuffs.
Principal Findings:
1. Volumetric Insights: Our analysis pinpointed the Optimum Asphalt Content (OAC) to be 5%.
2. Temperature Modulation: By harnessing the properties of natural Jordanian Zeolitic tuff, we achieved a substantial 30°C reduction in production temperatures.
3. Rutting Resistance Profiling:
o Asphalt mixtures fortified with 25% Zeolitic tuffs emerged as the best contenders for rutting resistance. This was evident from the reduced accumulated strain (170 µ) and heightened creep stiffness (12 Mpa).
o Such modified mixtures consistently demonstrated reduced strains and enhanced creep stiffness, emphasizing their improved rutting resistance capabilities.
4. Fatigue Resistance Dynamics:
o Mixtures enriched with 50% Zeolitic tuffs stood out in fatigue resistance performance, registering an impressive resilient modulus of 11000 Mpa.
o Relative to the control asphalt mixtures, these modified ones exhibited an increased resilient modulus, a testament to their superior stiffness and consequent fatigue resistance.
5. Legal and Environmental Context:
o Legal Infrastructure: Given the intricate dynamics of Jordan's construction industry, with its unique challenges and ever-evolving paradigms, the results accentuate the advantageous prospect of incorporating Zeolitic tuffs into asphalt mixtures, generating both economic and ecological dividends.
o Eco-conscious Leadership: Jordan's stalwart position on environmental preservation, solidified by its forward-thinking environmental framework, complements the research's alignment with sustainable, innovative alternatives to traditional asphalt.
6. Quality, Safety, and Compliance: The emphasis of the Jordanian Construction Law on safety, material excellence, and eco-friendliness finds a synergistic counterpart in applying Zeolitic tuffs. Their integration embodies Jordan's aspirations for a sustainable, safe, and compliant construction methodology.
7. Cognizance and Sustainable Acquisition: As the importance of knowledge dissemination becomes increasingly pivotal in Jordan’s construction sector, the research delineates a path toward sustainable procurement. Tapping into Zeolitic tuffs, a local treasure, represents a march towards a comprehensive, green, and legal construction paradigm.
RECOMMENDATIONS & FUTURE DIRECTIONS
1. Optimizing Zeolitic Tuff Percentage: Determining the ideal percentage of Zeolitic tuff for mineral filler is crucial to maximizing rutting and fatigue resistance.
2. Road Construction Insights: Construction using WMA augmented with 50% Zeolitic tuffs is recommended for roads with high traffic loads, particularly susceptible to fatigue cracking. Conversely, if rutting is the predominant concern, employing WMA with 25% Zeolitic tuffs would be optimal.
3. Paving the Way Forward: The results from this study underscore the potential advantages of transitioning to Zeolitic tuff modified mixtures over traditional Hot Asphalt Mix (HMA). Not only does this promise enhanced rutting and fatigue resistance, but it also suggests an elongated life cycle for flexible pavements.
4. Areas for Continued Research:
o Delving deeper into the performance dynamics of Zeolitic tuff-modified mixtures across a spectrum of temperatures, loads, and frequencies.
o Thoroughly investigating the ramifications of varied aggregate characteristics—ranging from grading and type to shape and hardness—on the longevity and durability of WMA mixtures.
5. Regulatory Resilience: It is imperative to recalibrate the environmental norms, especially in natural resource utilization like Zeolitic tuffs, eliminating any latent ambiguities.
6. Refined Oversight: Escalate surveillance and regulatory mechanisms to enshrine the unwavering adoption of eco-centric guidelines.
7. Cultivating a Knowledge Ecosystem: Champion concerted efforts towards fostering a collaborative ecosystem that synergizes collective wisdom, ensuring the ubiquity of best practices within the construction arena.
This research illuminates the myriad benefits of Zeolitic tuffs in warm asphalt mixtures and underscores the imperative of continued exploration in this domain.
LIST OF ABBREVIATIONS
HMA | = Hot Mix Asphalt |
WMA | = Warm Mix Asphalt |
SGC | = SUPERPAVE Gyratory Compactor |
OAC | = Optimum Asphalt Content |
CONSENT FOR PUBLICATION
Not applicable.
AVAILABILITY OF DATA AND MATERIALS
The data and supportive information are available within the article.
FUNDING
None.
CONFLICT OF INTEREST
The authors declare no conflict of interest, financial or otherwise.
ACKNOWLEDGEMENTS
Declared none.